Maximizing Business Efficiency with Premium Vacuum Membranes and System Components
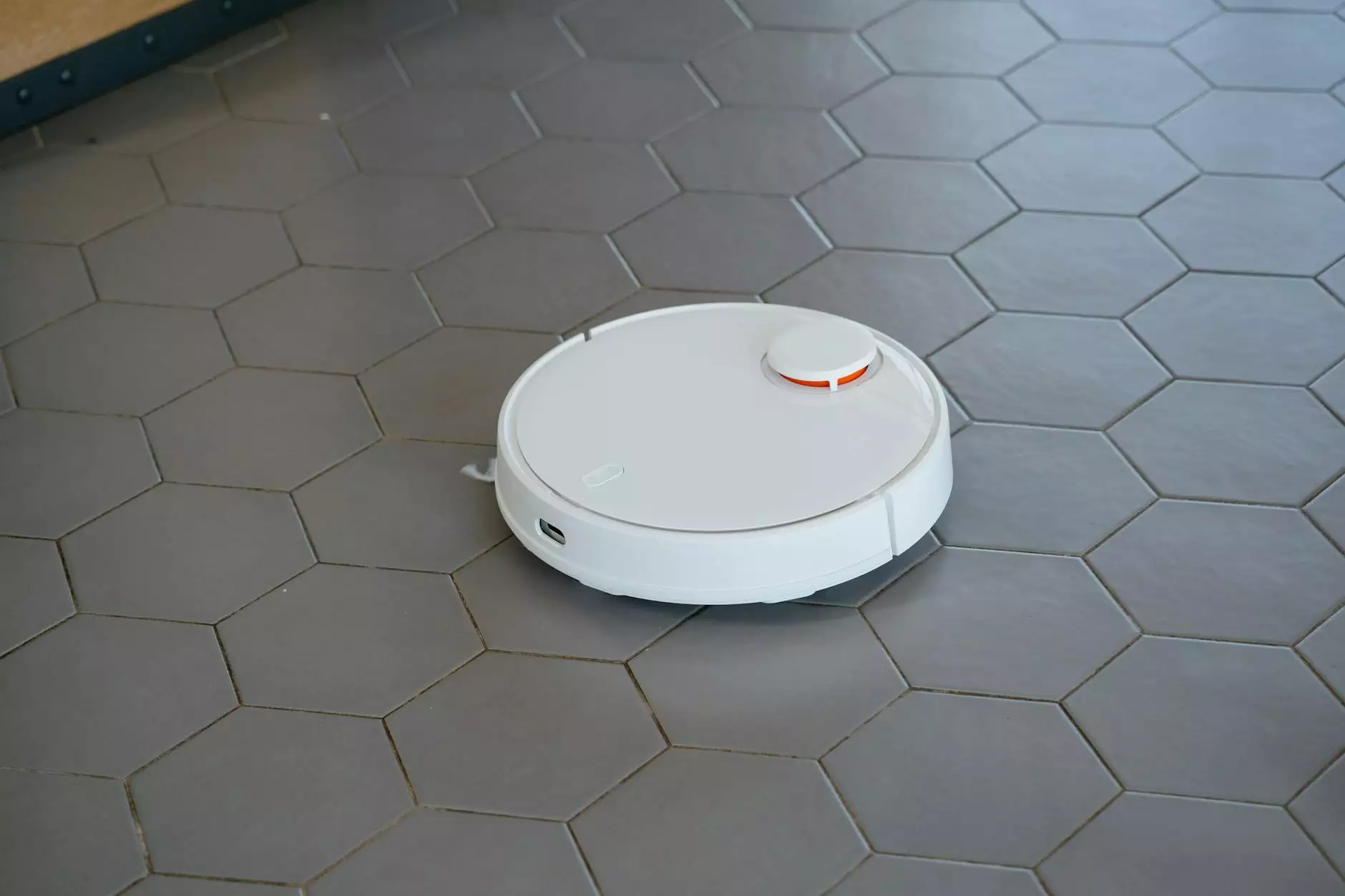
In the modern industrial landscape, the demand for precision, reliability, and efficiency has never been higher. Businesses involved in manufacturing, packaging, automation, and various other sectors rely heavily on advanced vacuum technologies to achieve optimal performance. Central to these systems are high-quality vacuum membranes, vacuum system parts, and specialized components such as the vacuum pump check valve. This comprehensive guide explores the critical aspects of these elements, providing invaluable knowledge for manufacturers, engineers, and procurement professionals aiming to elevate their operational standards.
Understanding the Importance of High-Quality Vacuum Membranes
Vacuum membranes are essential components in numerous industrial applications, serving as primary sealing, cushioning, or barrier elements within vacuum systems. Their quality and material composition directly influence the efficiency, durability, and safety of the entire setup. At vacuum-presses.com, a leading supplier, you will find an extensive selection of membranes tailored for diverse use cases.
Types of Vacuum Membranes and Their Industrial Applications
- Silicone Membranes: Known for their exceptional temperature resistance, flexibility, and chemical stability. Ideal for medical devices, food packaging, and high-precision manufacturing.
- Rubber Membranes: Offering excellent elasticity and sealing capabilities, often used in vacuum forming, embossing, and industrial automation.
- Natural Rubber Membranes: Valued for their natural elasticity, resilience, and cost-effectiveness, suitable for applications requiring high flexibility and durability.
Why Silicone Membranes Are the Material of Choice
Silicone membranes excel in environments demanding extreme conditions. They withstand high temperatures up to 300°C without degrading, making them invaluable in automotive, aerospace, and medical sectors. Additionally, they are resistant to ozone, UV light, and various chemicals, ensuring longevity and sustained performance.
The Significance of Rubber and Natural Rubber Membranes in Industry
Rubber-based membranes, especially natural rubber variants, offer outstanding elasticity and shock absorption. They are widely appreciated for their ability to maintain a tight seal under dynamic conditions, making them ideal in vacuum forming machinery and transport systems where flexibility and resilience are paramount.
Choosing the Right Vacuum System Parts for Your Business
Essential Vacuum System Components
- Vacuum Pumps: The heart of any vacuum system, responsible for creating and maintaining the vacuum environment.
- Vacuum Pump Check Valve: A critical component ensuring unidirectional flow, preventing backflow, and protecting the pump from potential damage during system shutdowns or power failures.
- Vacuum Reservoirs and Filters: Maintain stable vacuum levels and remove contaminants, ensuring system longevity.
- Seals and Gaskets: Vital for preventing leaks and maintaining system integrity.
The Critical Role of the Vacuum Pump Check Valve
The vacuum pump check valve is often overlooked but is fundamental to the reliable operation of vacuum systems. It acts as a safeguard, allowing air to flow in one direction—toward the vacuum pump—and preventing reverse flow that could compromise vacuum integrity or damage equipment.
Benefits of Using a High-Quality Vacuum Pump Check Valve
- Prevents Backflow: Ensures that atmospheric air does not infiltrate the vacuum system when the pump is off or during power outages.
- Protects the Pump: Shields the vacuum pump from potential damage caused by reverse pressure or sudden air influx.
- Maintains Stable Vacuum Levels: Contributes to continuous, consistent vacuum performance essential for high-precision processes.
- Reduces System Downtime: Minimizes maintenance needs by preventing system failures related to backflow issues.
Criteria for Selecting the Best Vacuum Pump Check Valve
Choosing the appropriate check valve involves understanding your system's specific needs. Consider the following factors:
- Material Compatibility: Ensure the valve is resistant to chemicals, oils, or other substances used in your process.
- Operating Pressure Range: Match the valve's pressure specifications with your system's requirements.
- Flow Rate: Select a valve that accommodates your system's airflow without causing restrictions.
- Size and Connection Type: Ensure compatibility with existing system fittings and space constraints.
Integrating Vacuum Membranes and Pump Components for Optimal Performance
To maximize efficiency and lifespan, a holistic approach should be adopted in system design and maintenance. This includes selecting appropriate membranes, system parts, and ensuring proper installation and regular inspections. Partnering with reputable suppliers such as vacuum-presses.com guarantees access to high-quality, durable components suited for demanding industrial environments.
Maintenance Tips for Vacuum Systems to Ensure Peak Performance
Sustaining efficient operation requires routine maintenance and prompt replacement of worn parts. Here are some practical tips:
- Regular Inspection of Membranes and Seals: Check for cracks, tears, or deterioration caused by chemical exposure or mechanical stress.
- Monitoring System Pressure: Use gauges to ensure vacuum levels are within designated ranges.
- Replacing the vacuum pump check valve: When signs of wear or malfunction appear, replace it immediately to prevent system failures.
- Cleaning Filters and Reservoirs: Remove debris or contaminants to maintain air quality and system efficiency.
- Scheduled Maintenance Checks: Follow manufacturer recommendations for systematic inspection and servicing.
Advancing Your Business with Innovative Vacuum Technologies
Staying ahead in competitive markets involves embracing technological advancements. Innovations in membrane materials, intelligent control systems, and energy-efficient vacuum pumps can significantly reduce operational costs and enhance process control. Working with suppliers who prioritize research and development helps integrate these innovations seamlessly into your operations.
Conclusion: Building a Robust Vacuum System for Long-Term Business Success
Investing in high-quality vacuum membranes, vacuum system parts, and critical components like the vacuum pump check valve is fundamental for achieving operational excellence. These elements not only ensure the reliability and efficiency of your processes but also contribute to safety, cost savings, and product quality. By understanding the nuances of each component and maintaining a proactive approach to system management, businesses can unlock new levels of productivity and growth.
At vacuum-presses.com, we are committed to providing top-tier vacuum solutions, including membranes, system parts, and expert support to help your business thrive in today's competitive environment. Embrace the power of superior vacuum technology and set your enterprise on the path to long-term success!