The Future of Manufacturing: Rapid Prototype Injection Moulding
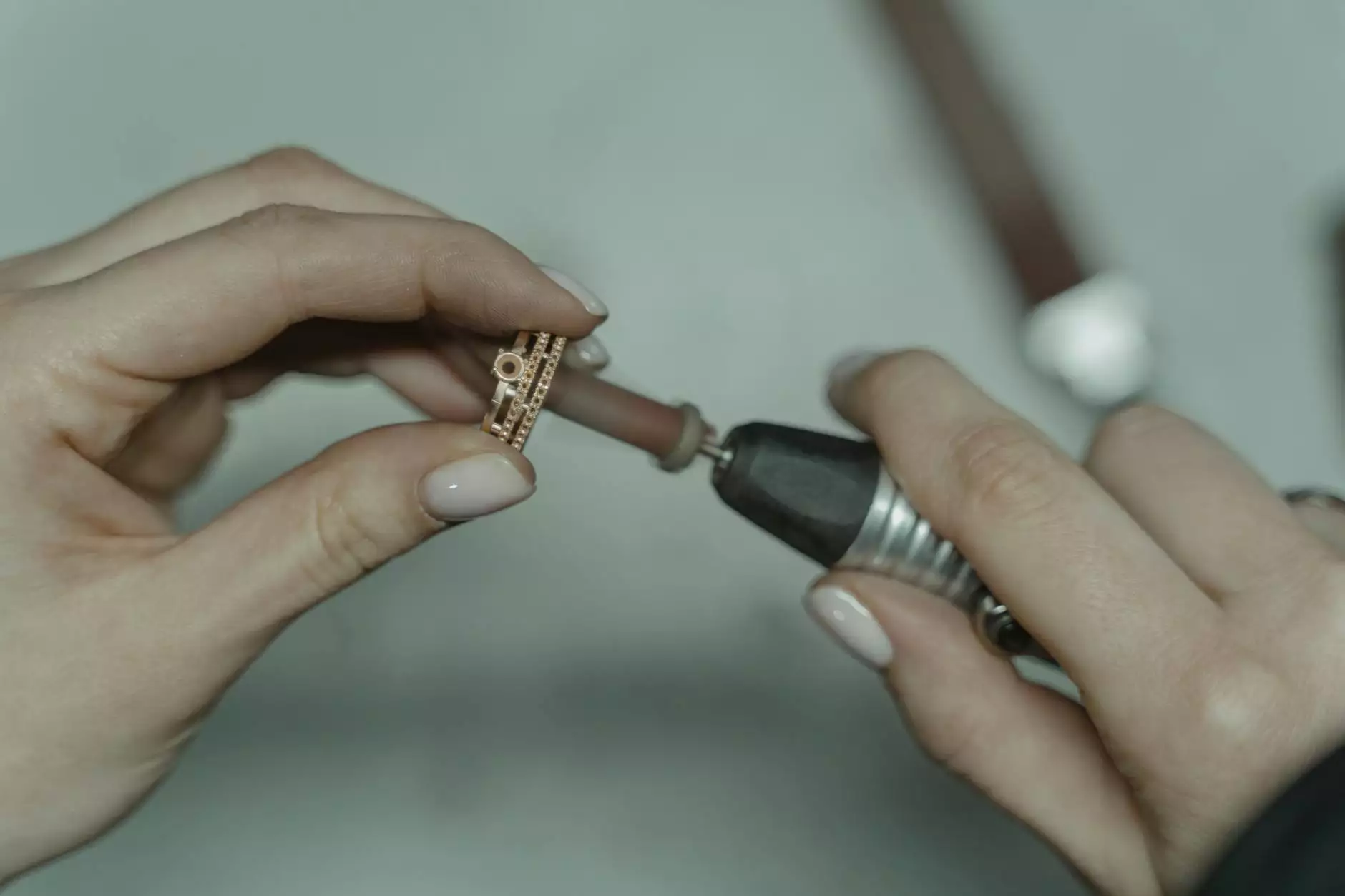
In today's fast-paced industrial environment, rapid prototype injection moulding stands out as a revolutionary technique that transforms product development and manufacturing processes. By significantly reducing the time and costs associated with traditional methods, it enables businesses to innovate faster and respond to market demands with agility.
Understanding Rapid Prototype Injection Moulding
At its core, rapid prototype injection moulding is a manufacturing process that allows engineers and designers to create prototype models quickly. This method uses advanced technologies and materials to produce high-quality prototypes that closely resemble the final product. Here's how it works:
1. The Process of Injection Moulding
- Design Creation: The process begins with a detailed design using CAD (Computer-Aided Design). Having an accurate digital model is vital for the subsequent steps.
- Mould Fabrication: Next, a mould is created, often using CNC machining or 3D printing techniques. This stage can be done quickly, allowing for faster iterations.
- Material Selection: Appropriate materials, typically thermoplastics or thermosetting plastics, are selected based on the product requirements.
- Injection Process: The chosen material is melted and injected into the mould under high pressure, ensuring precision and detail in the final product.
- Cooling and Ejection: After sufficient cooling, the prototype is ejected from the mould, ready for testing and evaluation.
2. Benefits of Rapid Prototype Injection Moulding
Choosing rapid prototype injection moulding comes with numerous advantages that can significantly benefit businesses across various sectors:
- Speed: The primary advantage is the swift production of prototypes. What used to take weeks can now be accomplished in days, or even hours.
- Cost-Efficiency: Reduces the costs associated with traditional prototyping methods, such as metal fabrication and extensive machining.
- Design Versatility: Supports a wide range of materials and complex geometries, making it suitable for diverse applications.
- Quality: Produces high-fidelity prototypes that mirror the physical and functional characteristics of the final product.
- Iterative Development: Facilitates rapid iterations and modifications based on testing feedback, ultimately leading to superior final products.
Applications of Rapid Prototype Injection Moulding
Industries around the world are harnessing the power of rapid prototype injection moulding for various applications, which include:
1. Automotive Industry
In the automotive sector, where innovation and precision are paramount, rapid prototypes are essential for testing new designs and technologies. This process can reduce time-to-market for new vehicle models while ensuring that safety and efficiency standards are met.
2. Consumer Electronics
The fast-paced world of consumer electronics demands rapid innovation. Companies can utilize rapid prototyping to test different designs and functionalities, allowing them to quickly introduce new products that cater to ever-evolving consumer preferences.
3. Medical Devices
The production of medical devices often involves stringent regulatory requirements. Rapid prototype injection moulding allows for the swift creation of prototypes that can be used for rigorous testing, ensuring they meet necessary safety and performance standards before full-scale production.
4. Aerospace and Defense
In aerospace and defense, precision is non-negotiable. Prototyping through rapid injection moulding ensures that components are not only high-quality but can also be developed in shorter cycles to keep pace in a competitive landscape.
How to Implement Rapid Prototype Injection Moulding in Your Business
Implementing rapid prototype injection moulding in your business can seem daunting, but understanding the process can simplify this transition. Here are the key steps:
1. Identify Your Needs
The first step is to pinpoint what you require from rapid prototyping. Determine the type of products you aim to develop, the materials needed, and any specific design characteristics.
2. Collaborate with Experts
Partnering with a manufacturer who specializes in rapid prototype injection moulding is crucial. They can provide insights and guidance through every stage of the process.
3. Prototype Development
Once you have the right team in place, the development of your prototype can begin. This will involve frequent communication to ensure that the prototype aligns with your vision and specifications.
4. Testing and Feedback
After creating the prototype, conduct rigorous testing to evaluate its functionality and performance. Gather feedback from users and stakeholders to refine the design.
5. Iteration
Use the insights gained from testing to make adjustments and improvements. Rapid prototype injection moulding allows for quick iterations, meaning you can evolve your design rapidly until you achieve optimal results.
Conclusion
In conclusion, rapid prototype injection moulding is a game-changer in the modern manufacturing landscape. Businesses that harness its capabilities can expect reduced development times, lower costs, and improved product quality. As industries continue to evolve, the importance of agility and innovation becomes ever more critical. Embracing rapid prototyping not only positions your company ahead of the curve but also empowers it to respond to market demands swiftly and effectively.
To explore these benefits further and discuss how DeepMould.net can assist your business in achieving its prototyping goals, don’t hesitate to contact us today!